- Case Studies
- December 5, 2024
The Role of Record Keeping in Business Operations
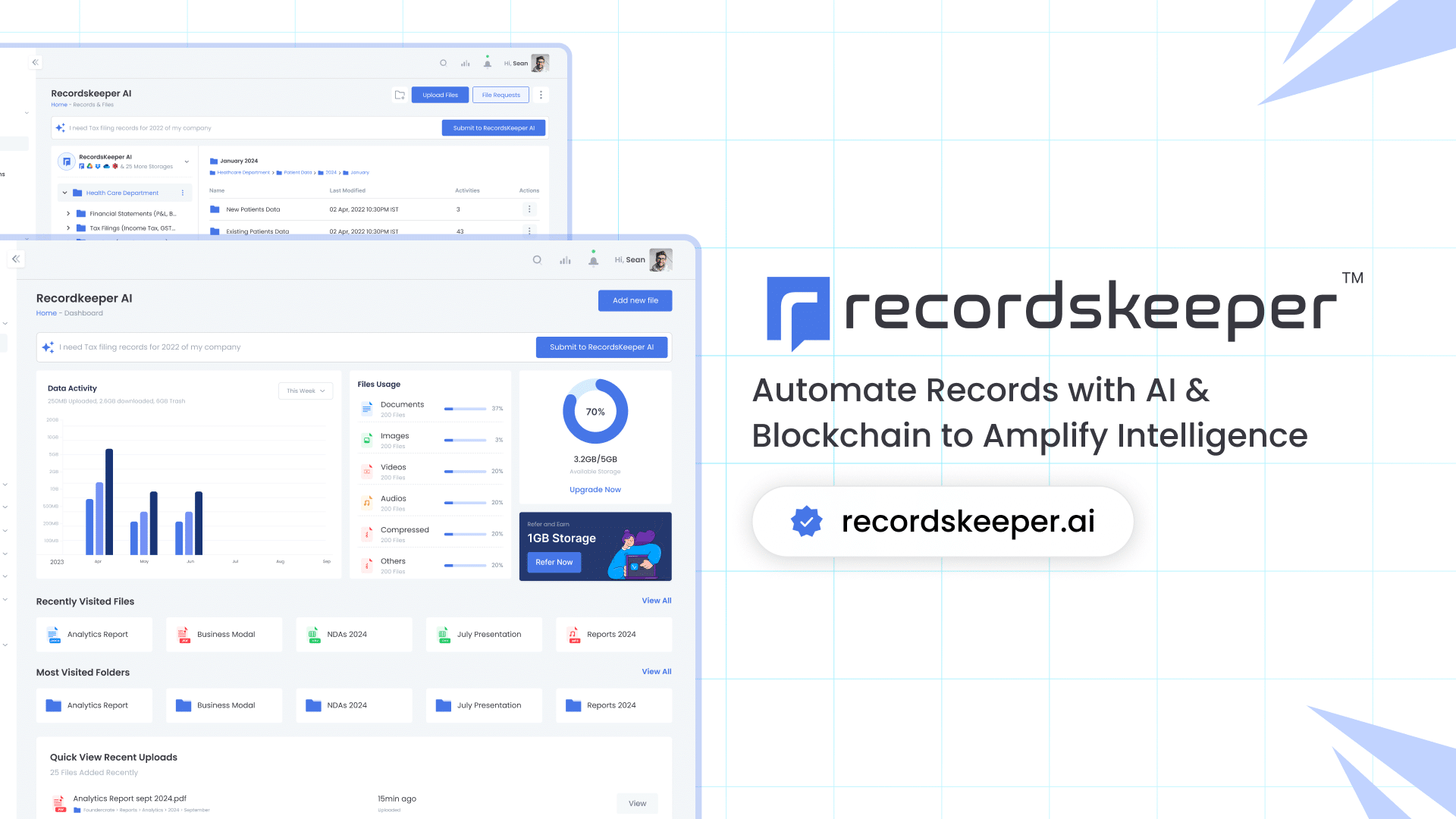
Record keeping, though often underestimated, is a cornerstone of business operations. Whether it’s for financial transactions, employee records, or inventory management, businesses of all sizes rely on organized documentation to make informed decisions, remain compliant with laws, and build a strong foundation for growth. In this case study, we examine how a medium-sized manufacturing company streamlined its record-keeping practices, leading to improved operational efficiency, better compliance, and enhanced decision-making.
Background: The Business
Company Name: XYZ Manufacturing Ltd.
Industry: Manufacturing
Employees: 150
Annual Revenue: $20 million
XYZ Manufacturing specializes in producing industrial machinery and components. Despite its growth, the company was facing several challenges related to inefficient record keeping. The company’s records were kept in paper form, scattered across different departments, which made it difficult to access key data quickly. This lack of organization often led to delays in financial reporting, inventory management issues, and compliance gaps.
Challenges Faced by XYZ Manufacturing
- Inefficient Data Access
Employees found it time-consuming to retrieve specific records, which hindered productivity and slowed down response times. - Compliance Issues
The company struggled to meet regulatory requirements due to inconsistent record-keeping practices, risking penalties and legal challenges. - Inventory Management Problems
Poor record-keeping led to inaccurate tracking of inventory, resulting in stockouts or overstocking, both of which affected customer satisfaction and profitability. - Inaccurate Financial Reporting
The lack of a centralized record-keeping system meant that the company’s financial reports were often inaccurate or delayed, complicating strategic decision-making.
The Solution: Implementing a Digital Record-Keeping System
To address these challenges, XYZ Manufacturing decided to adopt a comprehensive digital record-keeping system. The company implemented cloud-based software that integrated various departments, including finance, HR, inventory, and production. Key elements of the solution included:
- Centralized Digital Database: A single, cloud-based platform for storing and accessing all company records.
- Automated Data Entry: Automation tools for capturing data from invoices, receipts, and inventory logs.
- Access Control and Security: Permissions-based access to ensure only authorized personnel could view or modify sensitive records.
- Compliance Tracking: Built-in reminders and alerts to ensure compliance with industry regulations and tax laws.
- Real-Time Reporting: Tools for generating real-time financial and inventory reports, which helped improve decision-making.
Implementation Process
The implementation process took six months, during which XYZ Manufacturing worked with an IT consultant to ensure a smooth transition. Key steps in the process included:
- System Selection
After reviewing several options, XYZ Manufacturing chose a record-keeping software with customizable features that could scale with the company’s growth. - Data Migration
The company’s existing paper records were digitized and migrated to the new system. This required careful planning and validation to ensure data integrity. - Employee Training
Staff across various departments were trained on how to use the new system effectively. This ensured smooth adoption and reduced the risk of errors. - System Testing
Prior to full deployment, the system was tested for functionality and security. Feedback from employees was incorporated into the final setup. - Launch and Support
The new system went live, and a support team was available to address any issues that arose during the initial transition period.
Results: The Impact of Improved Record Keeping
After six months of using the new digital record-keeping system, XYZ Manufacturing saw significant improvements in several areas:
1. Improved Operational Efficiency
Employees were able to access records instantly, cutting down on the time spent searching for information. This led to faster decision-making and better overall productivity.
2. Enhanced Compliance
Automated alerts helped ensure that the company remained compliant with regulatory requirements. The company passed its next compliance audit with no issues, avoiding potential fines.
3. Better Inventory Management
With real-time tracking of inventory, XYZ Manufacturing was able to reduce stockouts by 30% and cut down on excess inventory by 15%. This resulted in better customer satisfaction and a reduction in storage costs.
4. Accurate Financial Reporting
The finance team was able to generate accurate financial reports in real-time, improving budget forecasting and strategic planning. This helped the company better allocate resources and manage cash flow.
5. Cost Savings
The move from paper to digital records eliminated the need for physical storage space, reducing overhead costs. Additionally, the increased efficiency led to time savings that were redirected toward revenue-generating activities.
Best Practices for Successful Record Keeping
Based on XYZ Manufacturing’s experience, here are some best practices for businesses looking to improve their record-keeping systems:
- Go Digital: Transition from paper to digital records to increase efficiency, reduce errors, and improve access.
- Choose the Right Software: Select record-keeping software that fits your business needs and can scale with growth.
- Implement Automation: Use automation tools to reduce manual data entry, which decreases the risk of human error and saves time.
- Train Employees: Ensure that employees are properly trained on the new system to ensure smooth adoption.
- Regular Audits: Perform regular audits of your record-keeping system to ensure compliance and accuracy.
Conclusion
Effective record keeping is not just a matter of organizing files; it’s a strategic asset that can help businesses optimize operations, ensure compliance, and make more informed decisions. As demonstrated by XYZ Manufacturing, a well-implemented digital record-keeping system can lead to significant improvements in efficiency, accuracy, and profitability. By adopting best practices and using the right tools, businesses can turn record keeping from a mundane task into a competitive advantage.
Archives
- December 2024
- November 2024
- October 2024
- September 2024
- August 2024
- July 2024
- June 2024
- May 2024
- April 2024
- March 2024
- February 2024
- January 2024
- December 2023
- November 2023
- October 2023
- September 2023
- August 2023
- July 2023
- June 2023
- May 2023
- April 2023
- March 2023
- February 2023
- January 2023
- December 2022
- November 2022
- October 2022
- September 2022
- March 2019
Want to get more content like this?
Signup to directly get this type of content to your inbox!!
Latest Post
Document Control in Manufacturing Plants
- December 21, 2024
Handling Rush Financial Report Requests
- December 20, 2024
Managing Record Access After Staff Changes
- December 19, 2024
Setting Up Temporary Project Archives
- December 18, 2024